What do the Internet of Things (IoT) and beer have in common? Well, there was the Budweiser Red Light, an automatic hockey light thats programmed to go off when your favorite team scores a goal. Then, there was Heineken Ignite, an interactive beer bottle that pulsates to the beat of the DJs music. But, the startup SteadyServ has created a beer related IoT app thats more than just a novelty. SteadyServs app, iKeg, saves bars time and money and helps distributors keep tabs on kegs and consumption levels. It even helps brewers know where and when their promotional dollars are turning into pints poured. Better yet, it ensures your favorite brew is always on tap and where to find it.
When Rob Tercek, a former creative director at MTV, was traveling with a layover in Indianapolis, he decided to grab a beer with longtime friend and local craft brewery co-owner Steve Hershberger. On a mission to serve his friend one of his own beers, it took Steve several bars to find one that had his beer on tap - bars that were supposed to have his inventory. "Im disappointed, Steve. This is a problem, why havent you solved it yet?"
the U.S. alone. Even with its rapid growth, the beer industry is one of the only "just in time" industries left. Knowing there is a huge market and an apparent problem that needed to be solved, Steve took on the challenge. SteadyServ was born.
A year later, the company has more than 4 patents pending, over $7.5 million in funding to date, and engineering teams working on hardware and software globally. The team has evolved through four prototypes to have a commercially ready, "Apple-simple" system that allows bar managers and beer sales reps to manage all of their keg orders on a smart phone.
At the National Beer Wholesalers Association (NBWA) in October, the incoming Chairman of the NBWA addressed the audience of over 5,000 attendees with a bold statement: "This isnt your grandfathers industry. It isnt your fathers industry. Change is upon us. Change is certain."
An Evolving Industry Even bar and restaurant owners have noticed that the beer industry has traditionally been slow to adopt new technology. "Were an industry that has been terribly resistant to change for probably 100 years. But were now ready and open for significant change," said Carl Bruggemeier, Vice Chairman of SteadyServ and CEO of The CZH Hospitality Group. "Our inventory management systems are very lacking. In many instances, we dont know what we have, we dont know how much we sell, and we dont know when we sell it. We lose sales because our customers want what we dont have."
Currently, the bar manager heads to the refrigerator to count kegs to see how many are left. He or she lifts each keg to see how full it is---essentially making the ordering process a guessing game. Ryan Kellerman, Director of Beverage and Hospitality for Scottys Brewhouse, says he spends a minimum of two and a half to two hours a week, per location, taking inventory in order to place their orders. Many managers are still using a pen and paper to collect information that impacts the business supply. If the beer rep doesnt get their order in time, the rep will place it for them-by guessing.
"Imagine if HP guessed at what Best Buy needed to fill its shelves on any given month without talking to the company or looking at any hard data," said Steve Hershberger, Chairman & CEO of SteadyServ Technologies.
"On average, according to many in the industry, approximately 20% of every beer order placed is wrong. How would you feel if every Amazon order you received was wrong?"
How it Works SteadyServs iKeg app completely changes how the industry does supply chain and inventory management; which benefits the bars themselves, distributors, brewers and, most importantly, us patrons.
Each keg is equipped with an RFID tag, which is attached to the keg just like a luggage tag. The tag information contains information like born on date, brewery name and delivery location. The keg also sits on top of a sensor. The sensor measures weight of the keg and how fast the weight is changing, which is a direct correlation to how much beer people are drinking. Keg information is paired with sales data, so the iKeg app knows exactly how much beer is poured and sold.
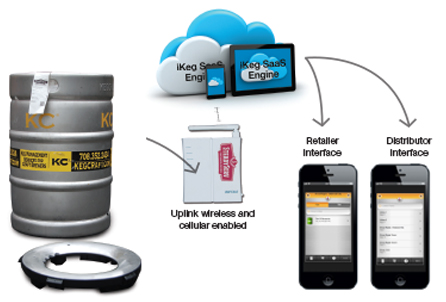
The keg data is collected from each kegs sensor and is aggregated by a ConnectPort Gateway. The gateway analyzes the data locally, then uses a Zigbee connection to get that data into the cloud. The iKeg application gathers information from the cloud and offers an interface that displays analytics for bar managers, distributors and eventually, patrons. "Our whole business is built around solving problems with data," said Joel Young, CTO of
Digi International, a company thats leading the way in Internet of Things solutions for businesses. "Who doesnt love that this solution can optimize operational efficiencies
and help people get more of their favorite beer?"
Your Favorite Tap at Your Fingertips Not only do bars save time, money and pain in counting and lifting kegs, theyre not losing money to unhappy customers who expect their favorite drafts to be in stock. A version of the app will also become available to the public, so we can see all of the places nearby that offer our favorite brews. Maybe a Foursquare integration is in the future? Currently, the system is in beta in the Midwest and will soon be expanding into other distributor franchises in the Midwest, South East and Western U.S. With another series of funding on the horizon, we should see the iKeg systems throughout North America within the next year. Heres to the Internet of Things, or the Internet of Thirst, for helping us never miss our favorite pint.